Metal Injection Molding
Metal Injection Molding, also called MIM, is a low cost, high volume manufacturing process that produces custom metal parts near to net shape. It combines the way injection molded plastics are formed with powdered metal sintering to create metal or ceramic parts which are stronger, denser and more capable of complex geometric shapes than most forged or die cast metal parts.
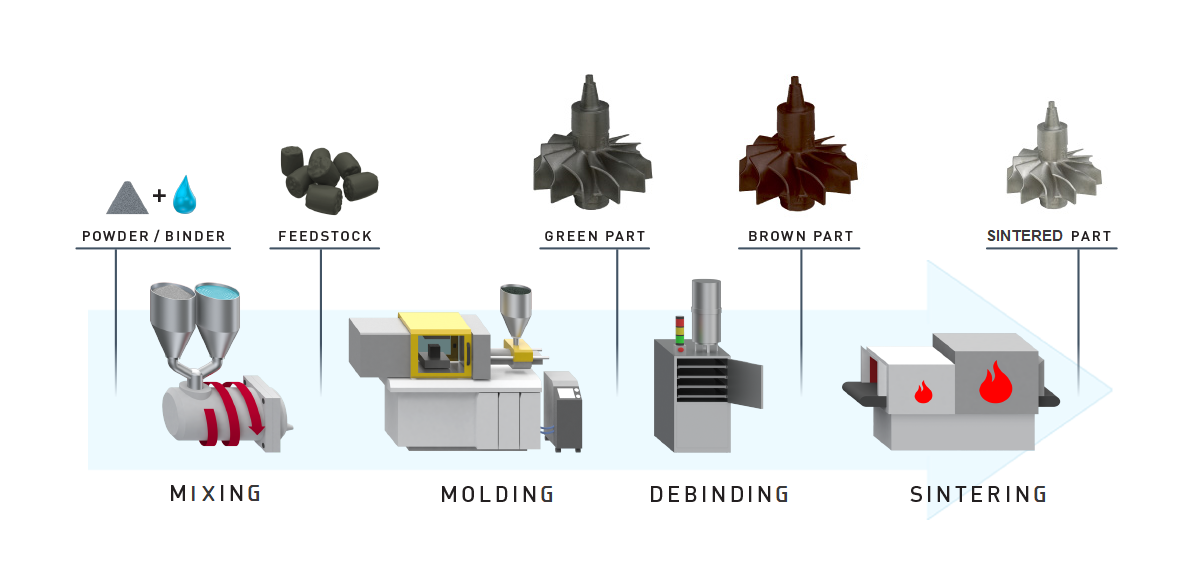
Mixing
Metal powders are mixed with thermoplastic polymers and waxes (binder) using heat to form a mixture in which every metal particle is uniformly coated. Once the mixture cools, it’s granulated to form the feedstock for the injection molding machines.
Molding
The feedstock is fed into the injection molding machines where heaters melt the binder to a toothpaste-like consistency and push it into the mold. The resulting part, once cooled, is ejected from the mold. Runners and gates are removed at this time so that that material can be recycled.
Debinding
The “green part” still contains both the original metal and binder material that made up the feedstock. It is approximately 20% larger than the finished part will be. Now a specific portion of the binder must be removed. This is usually accomplished either thermally or chemically, depending on the material being process. FineMIM employs both technologies and each use is dependent of the product being produced. The resulting debound part is referred to as a “brown part.”
Sintering
The brown part is placed in a furnace and heated to within 85% of the metal’s melting temperature. The remaining binder is removed and the metal particles fuse together, shrinking to form a solid metal part that is nearly full dense (as compared to wrought density) and meets the desired design specifications. The sintered metal component can then be further processed through machining, plating, heat treating, polishing, PVD, etc., if necessary, similar to that of a machined part.